The Most Common Mechanical Tests For Production: Ensuring Your Design Is Ready for Manufacturing
- Jared Haw
- Mar 2
- 11 min read
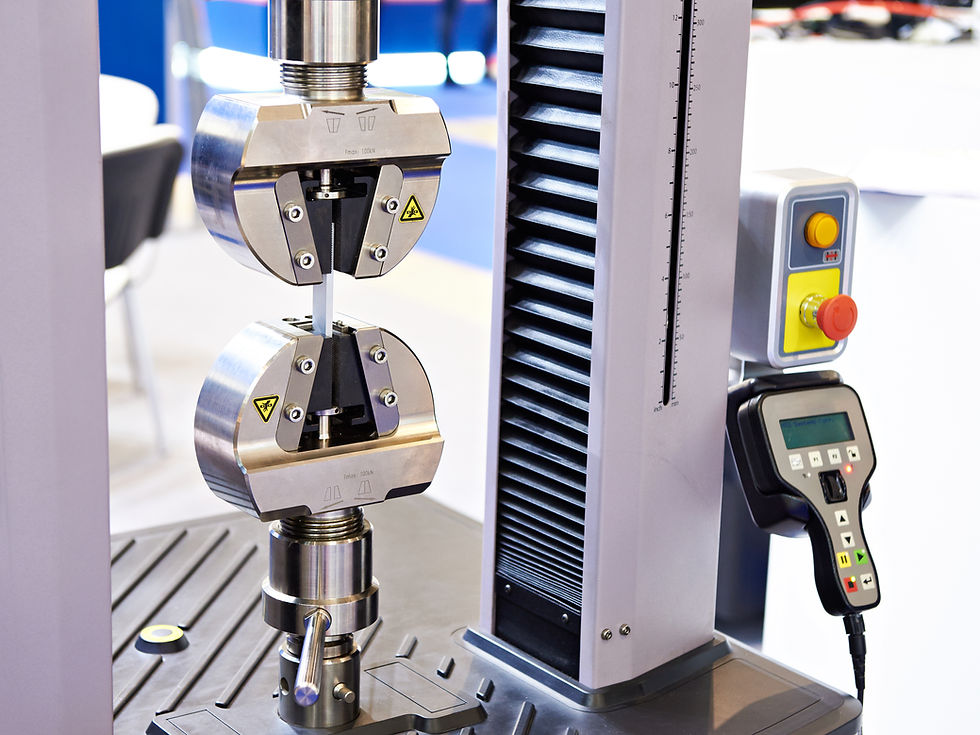
Before taking a product into mass production, it’s important to ensure that its design will perform as intended under real-world conditions. Mechanical testing serves as a key step in this validation process, offering valuable insights into how materials and components will behave when subjected to stress, pressure, or wear. These tests help identify potential issues early in the design phase, allowing for necessary adjustments before mass production begins.
Skipping these tests can lead to major consequences. Without proper verification, products may fail in the market, resulting in costly recalls, refund requests, and negative customer reviews. Such failures can damage a brand’s reputation, increase production costs, and delay time-to-market. By conducting these mechanical tests, manufacturers can significantly reduce the risk of failure, ensuring a product that meets performance, safety, and durability expectations.
Here are the top mechanical tests for production.
Tensile Test
The tensile test is one of the most common mechanical tests conducted to assess the strength and flexibility of materials. It measures how a material behaves when it is stretched or pulled apart, providing valuable data about its tensile strength, elongation, and ductility.
During this test, a sample of the material is subjected to increasing tension until it breaks, and key properties like the maximum force it can withstand before failure, are recorded.
Key Insights of Tensile Tests
The results of a tensile test reveal important characteristics of the material:
Tensile Strength: The maximum amount of stress a material can endure before breaking.
Elastic Modulus: The material's ability to return to its original shape after the stress is removed.
Elongation: How much the material stretches before breaking, indicating its ductility.
Understanding these properties helps determine whether the material is suitable for its intended application. For example, materials with high tensile strength are often used in structural applications where durability and resistance to breakage are critical.
When To Use The Tensile Tests
Tensile testing is crucial for consumer products that experience pulling forces, such as:
Smartphone charging cables: Ensuring they don’t break easily with repeated use.
Wearable fitness bands: Testing elasticity and durability under stretching.
Plastic packaging films: Verifying resistance to tearing when pulled.
By performing tensile tests, manufacturers can ensure that their products won’t fail under normal usage conditions, reducing breakage complaints and product returns.
Compression Test
The compression test evaluates how a material or component behaves when subjected to compressive forces, or forces that push or squeeze it. As you can guess, this is the opposite of the tensile test.
The compression test is important to understand a material’s ability to withstand forces that could lead to crushing, buckling, or permanent deformation. During the test, a sample is placed between two plates, and force is gradually applied to compress the material until it deforms or breaks. The test provides data on the material's resistance to compression as well as its potential for failure under pressure.
Key Insights of Compression Test
The results of a compression test offer insights into several key material properties:
Compressive Strength: The maximum compressive force a material can withstand before failing.
Elastic Deformation: The ability of a material to return to its original shape after being compressed.
Plastic Deformation: How much permanent deformation occurs after the material reaches its yield point.
Brittleness or Ductility: Whether the material will fracture or bend under stress.
Compression tests can also reveal how materials behave under different conditions, such as high-pressure environments, and can help determine whether they will buckle, crack, or compress uniformly under load.
When To Use The Compression Test
Compression testing is valuable for consumer products that face pressure or stacking, such as:
Plastic bottles: Ensuring they don’t collapse when stacked in warehouses or shipping containers.
Foam packaging: Testing how well it absorbs shocks and protects fragile products.
Luggage and backpacks: Checking if they can handle the pressure from being packed tightly.
By conducting compression tests, manufacturers can prevent issues like crushed packaging, deformed containers, or weakened product structures that lead to poor customer experiences.
Impact Test
The impact test evaluates a product’s ability to absorb energy from sudden shocks, drops, or collisions. This test is crucial for ensuring that a product can handle real-world use without breaking or becoming unsafe. Manufacturers use impact testing to identify weak points in a design and improve product durability before mass production.
Key Insights of Impact Test
A product’s ability to withstand impact is directly related to its material properties and design. If a product is too brittle, it may crack or shatter upon impact, leading to potential safety hazards. On the other hand, if it is too soft, it may deform easily and lose functionality. Impact testing helps strike a balance between durability and usability.
Toughness: This measures how much energy a material can absorb before it breaks. Products with high toughness can survive everyday drops or bumps without immediate failure.
Shatter Resistance: Some materials, such as glass or rigid plastics, can break into sharp pieces when impacted. Testing ensures that a product remains safe and intact even after accidental drops.
Durability in Daily Use: Frequent drops or rough handling can weaken a product over time. Impact testing helps manufacturers verify that their products maintain strength and reliability over prolonged use.
When To Use the Impact Test
Many consumer products must withstand impacts as part of normal use. Whether it’s an electronic device that gets dropped, a suitcase tossed onto a conveyor belt, or a child’s toy that experiences rough handling, impact resistance is a key factor in product reliability. Testing ensures that products remain functional and safe despite these everyday challenges.
Smartphones and protective cases: Phones are among the most frequently dropped consumer products. Impact testing ensures that screens, casings, and internal components can survive common drops from various heights.
Children’s toys: Kids tend to drop, throw, and step on their toys. Testing ensures that toys won’t break into small, hazardous pieces that could pose choking risks.
Luggage and suitcases: Travel gear experiences frequent impacts from baggage handling. Testing ensures that suitcases and their handles, zippers, and wheels don’t break under normal travel conditions.
Household appliances: Items like blenders, coffee makers, and vacuum cleaners may be accidentally dropped. Impact testing ensures they remain functional and don’t crack or shatter easily.
By conducting impact tests, manufacturers can minimize product failures, reduce warranty claims, and improve customer satisfaction by delivering more durable and reliable products.
Fatigue Test
The fatigue test evaluates how a product or material performs under repeated stress over time. Unlike a single impact or compression test, fatigue testing simulates the wear and tear a product will experience throughout its lifecycle. Repeated loading, bending, or twisting can weaken materials, leading to unexpected failures if not properly tested. This test helps manufacturers identify weak points and improve long-term durability before a product reaches consumers.
Key Insights of Fatigue Test
Products that experience continuous or repeated stress must be able to withstand these forces without cracking, deforming, or breaking. Fatigue testing helps predict how long a product will last under normal use and ensures it won’t fail prematurely. By identifying weaknesses early, manufacturers can make design or material adjustments to extend a product’s lifespan.
Resistance to Repeated Stress: Some materials may perform well in one-time strength tests but degrade under repeated use. Fatigue testing ensures that products remain reliable over extended periods.
Crack and Fracture Prevention: Small cracks can develop from repeated stress, leading to sudden failures. This test helps manufacturers identify materials prone to fatigue-related fractures.
Durability in Everyday Use: Many consumer products experience frequent movements, bending, or pressure. Fatigue testing ensures they maintain their structural integrity under normal wear and tear.
When To Use the Fatigue Test
Many consumer products go through cycles of bending, stretching, or repeated force application in everyday use. Without fatigue testing, these products may degrade faster than expected, leading to warranty claims and dissatisfied customers.
Hinges on laptops and foldable devices: The repeated opening and closing of a laptop or foldable phone can weaken the hinges over time. Fatigue testing ensures they remain functional after thousands of cycles.
Wearable devices and fitness bands: These products are constantly flexed and stretched on the wrist. Testing confirms that materials won’t crack or lose elasticity with daily use.
Plastic packaging with snap closures: Clips, hinges, or fasteners on packaging can break after repeated opening and closing. Fatigue testing ensures they remain secure over multiple uses.
Automotive and bicycle components: Parts like pedals, brake levers, and suspension components experience repeated stress. Fatigue testing ensures they don’t fail unexpectedly due to prolonged use.
By performing fatigue tests, manufacturers can prevent premature product failures, improve reliability, and enhance customer satisfaction. This ensures that products maintain their performance and durability throughout their intended lifespan.
Hardness Test
The hardness test measures a material's resistance to deformation, scratches, or dents. This is particularly important for consumer products that experience frequent contact with other surfaces or need to maintain their shape and appearance over time. By determining how hard or soft a material is, manufacturers can ensure that their product will withstand daily wear and tear without excessive damage.
Key Insights of Hardness Test
Hardness is directly related to a product’s durability and resistance to external forces. A material that is too soft may dent or wear down quickly, while one that is too hard may be brittle and prone to cracking. Finding the right balance helps manufacturers create products that are both strong and long-lasting.
Scratch and Wear Resistance: Harder materials are less likely to get scratched or show signs of wear, making them ideal for high-use items like smartphones and kitchen appliances.
Structural Integrity: A material’s hardness affects its ability to maintain its shape under pressure. Testing ensures that products don’t deform easily during everyday use.
Protection Against Dents and Indentations: Products that experience frequent contact, such as tools or consumer electronics, need a surface that resists permanent indentations.
When To Use The Hardness Test
Many consumer products need to maintain their appearance and structural integrity despite frequent handling. Hardness testing helps ensure that surfaces remain smooth, resistant to damage, and durable over time.
Smartphone screens and cases: Screens need to be hard enough to resist scratches from keys and coins, while cases must prevent dents and wear from daily drops.
Cookware and kitchen utensils: Pots, pans, and knives require hardness to resist scratches from metal utensils and cleaning tools.
Eyewear and sunglasses: Lenses need to be hard enough to resist scratches while remaining shatter-resistant for safety.
Flooring and furniture surfaces: Materials like laminate, wood, and plastic coatings must resist dents and wear from daily foot traffic or heavy objects.
By conducting hardness tests, manufacturers can improve product longevity, reduce visible wear over time, and ensure a high-quality appearance even after extended use.
Shear Test
The shear test evaluates a material’s ability to resist forces that cause layers to slide against each other. This type of stress occurs when two connected parts experience opposing forces, which can lead to deformation or failure if the material is not strong enough. Shear testing is crucial for products with fasteners, adhesives, or layered materials to ensure they can withstand real-world use without breaking apart.
Key Insights of Shear Test
Shear strength plays a critical role in determining how well materials hold up under opposing forces. If a material or adhesive has low shear resistance, it can fail when subjected to sideways pressure, leading to product malfunction or breakage. Testing helps manufacturers select the right materials and bonding methods for long-term reliability.
Joint and Fastener Durability: Screws, bolts, and adhesives must withstand shear forces without breaking or coming loose. Testing ensures secure connections in consumer products.
Layered Material Strength: Many products, such as laminated plastics or composite materials, rely on multiple layers. Shear testing confirms that these layers stay intact under stress.
Structural Stability Under Load: Shear forces occur when parts of a product experience shifting forces, such as a handle attached to a base. Testing ensures that critical joints do not fail under pressure.
When To Use The Shear Test
Consumer products that involve adhesives, layered materials, or mechanical fasteners must resist shear stress to ensure durability and safety. Shear testing helps manufacturers confirm that materials won’t fail under normal use conditions.
Adhesive-backed products: Items like phone screen protectors, stickers, and industrial adhesives need to resist peeling or sliding under stress.
Eyewear frames and hinges: The joints connecting arms to glasses experience shear stress with repeated opening and closing. Testing ensures they remain secure over time.
Plastic and metal casings: Laptops, appliances, and electronic enclosures use clips or screws that must hold under shear stress without separating.
Sports and outdoor gear: Items like climbing harnesses, bicycle pedals, and snowboard bindings must withstand shear forces to prevent unexpected failures.
By performing shear tests, manufacturers can improve product safety, ensure long-lasting performance, and reduce the risk of failure due to weak joints or adhesive bonds.
Creep Test
The creep test evaluates how a material deforms over time when exposed to continuous stress, especially under high temperatures. Unlike immediate failures caused by impact or fatigue, creep occurs gradually, making it a critical test for products that need to maintain their shape and functionality over extended use. This test helps manufacturers ensure that materials won’t warp, stretch, or fail when subjected to prolonged stress.
Key Insights of Creep Test
Materials that experience constant pressure or load can slowly deform, which can affect a product’s performance and safety. Creep testing helps identify materials that may lose strength or shape over time, allowing manufacturers to make necessary adjustments before mass production.
Long-Term Load Resistance: Ensures that products remain functional and structurally sound even after years of use under steady pressure.
High-Temperature Performance: Some materials weaken when exposed to heat, causing deformation over time. Testing verifies their stability under different environmental conditions.
Prevention of Warping and Stretching: Materials prone to creep may become misshapen, reducing their effectiveness and leading to potential product failures.
When To Use Creep Test
Consumer products that experience constant pressure, weight, or heat exposure must undergo creep testing to ensure long-term durability. Without this test, materials may gradually fail, leading to product malfunctions or safety issues.
Plastic and rubber components: Items like phone cases, rubber seals, and appliance parts can slowly deform under prolonged stress, reducing their effectiveness.
Furniture and seating materials: Chairs, cushions, and foam padding must resist slow compression to maintain comfort and shape.
Electronics under heat exposure: Devices like laptops and gaming consoles generate heat, which can cause plastic casings or solder joints to weaken over time.
Medical devices and wearables: Braces, prosthetics, and fitness bands must retain their shape and support despite continuous pressure on the body.
By conducting creep tests, manufacturers can prevent gradual material failure, improve product reliability, and ensure that products perform as expected over their intended lifespans.
Thermal Expansion Test
The thermal expansion test measures how a material’s size changes in response to temperature variations. Materials expand when heated and contract when cooled, and understanding how a product reacts to temperature changes is crucial for ensuring its durability in various environments. This test helps manufacturers confirm that materials won’t warp, crack, or deform due to temperature fluctuations over time.
Key Insights of Thermal Expansion Test
Thermal expansion can impact a product’s performance, especially in environments with significant temperature swings. If a material expands or contracts too much, it can lead to misalignments, cracks, or other types of failure. Testing allows manufacturers to choose materials that will maintain their form and functionality across a range of temperatures.
Precision in Tight Tolerances: Products with moving parts, like electronic devices or mechanical tools, must maintain precise dimensions even as temperatures change.
Material Compatibility: When combining different materials, it's important to ensure they expand and contract at similar rates. A mismatch can lead to stress at the joints and eventual failure.
Environmental Durability: Products exposed to varying temperatures, such as outdoor gear or automotive parts, need materials that can handle thermal changes without losing integrity.
When To Use The Thermal Expansion Test
Thermal expansion testing is essential for products designed to operate in environments with fluctuating temperatures or those made from materials that may experience heating or cooling. Without this test, products might not perform correctly or could experience premature failure.
Electronics and gadgets: Laptops, smartphones, and other electronic devices often experience heat from internal components. Thermal expansion testing ensures that the casing, circuits, and components maintain their shape and fit.
Automotive parts: Engine components, exhaust systems, and sensors must withstand temperature changes from heat exposure while retaining their structural integrity.
Outdoor gear: Products like tents, sleeping bags, and thermoses experience temperature shifts, and their materials must expand and contract without compromising performance.
Plumbing and piping systems: Pipes, fittings, and connectors in plumbing systems must resist expansion and contraction with temperature changes to prevent leaks and cracks.
By performing thermal expansion tests, manufacturers can ensure that their products remain reliable, functional, and safe in varying temperature conditions, thus improving longevity and customer satisfaction.
Conclusion: Mechanical Tests For Production
Mechanical testing is a crucial step in ensuring that your product is ready for the market and performs as intended under real-world conditions. From tensile and compression tests to thermal expansion and fatigue testing, each test provides valuable insights into a product's durability, strength, and long-term reliability. By investing in these tests, manufacturers can prevent costly product failures, reduce the risk of returns, and protect their brand reputation.
Failing to conduct these essential tests may result in unexpected failures, leading to dissatisfied customers, negative reviews, and expensive recalls. Ensuring that products meet the necessary standards before production can save both time and money in the long run, while also ensuring that consumers receive high-quality, reliable products that perform as expected. Whether you're designing gadgets, outdoor gear, or consumer appliances, proper mechanical testing is key to creating a product that stands the test of time.
Comments