T0, T1, T2: A Guide to Plastic Injection Molding Sample Stages
- Jared Haw
- Feb 18
- 5 min read
Updated: Apr 7
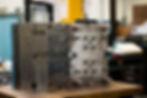
Maybe your supplier just told you that the T0 samples will be ready next week. But do you know what that means? If you’re new to plastic injection molding, terms like T0, T1, and T2 can feel like insider jargon. However, these designations are key milestones in the die-making process which mark different stages of molding testing and refinement.
Each of these molding trial runs helps you to identify issues, improve part quality, and ensure the mold is production-ready. Understanding what to expect at each stage will help you better communicate with your supplier, manage project timelines, and set realistic expectations for final production. In this blog, we’ll break down what T0, T1, T2, and beyond really mean, so you can confidently navigate the injection molding process.
What Do T0, T1, T2 Mean in Injection Molding?
In plastic injection molding, T0, T1, and T2 refer to different stages of mold trials, each trial representing a key step in enhancing the mold and ensuring the final part meets design and quality requirements. These trial runs allow manufacturers to test the mold, identify issues, and make adjustments before moving into full production.
The "T" in TO, T1, and T2 stands for "trial," with each stage marking a new iteration of testing. T0 is the very first shot from the mold, typically used for an initial evaluation of mold functionality. T1 follows as the first customer-facing sample, incorporating early refinements. T2 and subsequent trials continue improving dimensional accuracy, surface finish, and overall part quality.
Understanding these stages is essential for managing expectations and communicating effectively with your supplier. The number of trial runs needed depends on factors such as part complexity, material selection, and mold performance. In some cases, multiple iterations beyond T2 may be required to fine-tune the process before final approval for mass production.
T0: The First Trial (Initial Sample Evaluation)
T0 is the very first test run of a new injection mold, marking the initial step in evaluating how well the mold performs. At this stage, the goal is to produce sample parts directly from the mold without making any fine-tuned adjustments. These first shots provide critical insights into the overall mold design, material flow, and any major defects that need to be addressed before moving forward.
Since T0 samples are typically produced as soon as the mold is capable of forming parts, they often have noticeable imperfections. These can include dimensional inaccuracies, short shots (where the mold doesn’t fill completely with the molten resin), warping, sink marks, or flashing. At this point, engineers will analyze the results to identify whether modifications are needed for the mold itself, the injection parameters, or even the material selection.
T0 samples are not intended for full functional testing or customer approval. Instead, they serve as an internal checkpoint for the manufacturer to ensure that the mold is operating as expected before proceeding to the next stage. Depending on the complexity of the part, multiple iterations of T0 may be necessary before moving on to T1.
T1: The First Official Sample (Refinement Begins)
T1 marks the first official trial where the molded part is evaluated for customer review. Unlike T0, which is primarily an internal test, T1 samples are meant to provide an initial look at how well the mold produces parts under standard conditions. At this stage, the mold has undergone some initial adjustments based on T0 results, but it is still not fully optimized.
The goal of the T1 trial is to assess key factors such as dimensional accuracy, surface finish, and overall part functionality. While the part may closely resemble the final product, it’s common for minor defects to appear, such as slight warping, sink marks, or variations in tolerance. These early imperfections provide valuable feedback, helping engineers determine what additional mold modifications or process adjustments are necessary.
Customers receiving T1 samples should carefully review them and provide detailed feedback to the manufacturer. If critical issues are found, further refinements will be made before moving on to T2, where the part should be much closer to production-ready quality.
T2: Fine-Tuning and Pre-Production Readiness
T2 represents a more refined stage in the injection molding process, where the mold and production parameters have been adjusted based on feedback from the T1 trial. At this point, the goal is to produce samples that are much closer to final production quality, with improved dimensional accuracy, surface finish, and overall part consistency.
During the T2 trial, manufacturers fine-tune processing conditions such as injection pressure, cooling time, and material flow to ensure repeatability in mass production. Any remaining minor defects, such as slight shrinkage, cosmetic imperfections, or tolerance deviations, are addressed to bring the part within specification.
T2 samples are often used for more advanced testing, including functional validation, assembly fit checks, and even limited pilot runs. If the parts meet all quality and performance requirements, the mold may be approved for production. However, for complex parts or critical applications, additional trials (T3 and beyond) may still be required to achieve full production readiness.
T3 and Beyond: Final Adjustments and Production Approval
T3 represents the final round of mold trials before full-scale production begins. By this stage, the mold has undergone multiple refinements based on feedback from previous trials, and the goal is to confirm that all parts meet the required specifications with consistency and repeatability. T3 samples should closely resemble production-quality parts, with minimal to no defects, stable dimensional accuracy, and an optimized molding process.
At this point, manufacturers conduct final validations, which may include extensive functional testing, assembly verification, and stress testing. If the parts pass these final checks, the mold is approved for mass production. However, in some cases, especially for complex designs or highly regulated industries, further trials (T4, T5, etc.) may still be required to fine-tune the process or validate new materials.
Reaching the T3 stage (or beyond) is critical for ensuring a smooth transition into full production. This final approval step minimizes the risk of defects in large production runs, reduces costly rework, and guarantees that the product meets all quality and performance expectations.
Conclusion
Understanding the different stages of plastic injection molding trials, T0, T1, T2, and beyond, can help you set realistic expectations and communicate more effectively with your supplier. Each stage plays a critical role in refining the mold, identifying potential issues, and ensuring that the final product meets quality and performance standards.
While it may be tempting to rush through these trials, taking the time to properly evaluate each iteration leads to a more reliable and cost-effective production process. Whether you’re reviewing your first set of T0 samples or approving T3 for mass production, knowing what to expect at each step will help you make informed decisions and keep your project on track.
If you’re working with a supplier on a new injection-molded part, ask about their trial process and be prepared to provide detailed feedback at each stage. A well-managed molding process results in better parts, fewer production delays, and a smoother manufacturing experience overall.
Are you looking for a reliable partner for your plastic injection molding needs? We would be happy to discuss your needs with you. Email us at Hello@epowercorp.com today to discuss your project and get started!