Pricing and Currency: How Tariffs Affect Manufacturing Costs
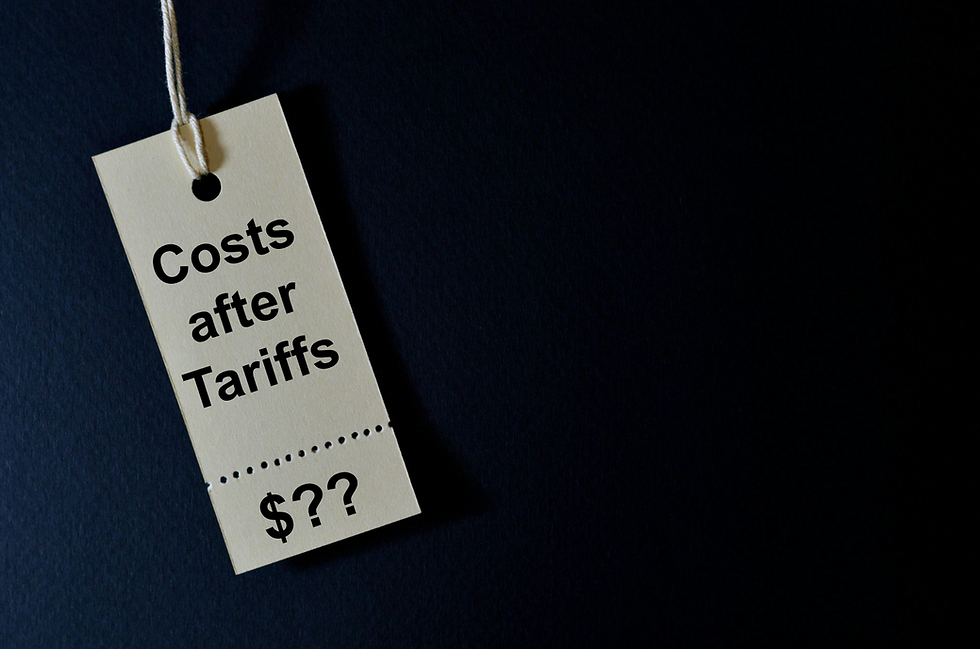
Understanding how tariffs affect manufacturing costs is crucial for businesses with a global supply chain. When governments impose tariffs, the assumption is that the tariffs will cause inflation. However, this is a common misconception. While tariffs increase costs for importers and manufacturers, their broader impact on inflation is a bit more complex. For example, studies done by the Economic Policy Institute show that tariffs don’t cause inflation.
Instead of focusing on inflation, this article will share how tariffs influence the pricing for both manufacturers and suppliers and how these tariffs cause fluctuations in exchange rates. When tariffs disrupt global trade dynamics, they can shift exchange rates, impacting the cost of raw materials, labor, and production. By understanding these relationships, manufacturers, and businesses can better anticipate and navigate the challenges posed by shifting trade policies.
How Tariffs Impact Product Pricing
The Council on Foreign Relations states that a tariff is a tax imposed on foreign-made goods, paid by the importing business to its home country’s government. So, think about the tariffs imposed on goods made in China and how the price will be affected.
When tariffs are applied to raw materials, components, or finished goods, manufacturers often face higher costs. These added expenses can impact businesses in multiple ways.
For domestic producers relying on imported materials, such as metals, plastics, or electronic components, a tariff will raise the price they must pay for these inputs. Thus, increasing the price for the end consumer, even if the majority of assembly is done in the US (or the home country). Manufacturers then have to decide whether to absorb these additional costs, reduce margins, or pass them on to customers by increasing prices.
For those manufacturing overseas, such as China, U.S. companies face higher costs, which directly impact their pricing strategies. Some businesses absorb these costs, while others pass them on to consumers. The companies that are manufacturing in China with tariffs paid on the final product and the domestic supplier paying more for inputs have ultimately the same pricing strategy questions looming over their head.
Additionally, the Chinese government may respond to tariffs by adjusting monetary policies or allowing the yuan to weaken. Thus making the dollar stronger which can reduce the price of products coming out of China.
These tariffs highlight the importance of the need to quickly migrate your supply chain. With this, you can quickly move production to a country without tariffs or try to re-shore manufacturing. However, for businesses that cannot easily switch suppliers or shift production, the impact can be significant.
Tariffs also influence pricing beyond direct manufacturing costs. They disrupt supply chains, increasing uncertainty and sometimes leading to excess inventory, shortages, and production delays. These factors can further drive up prices, as companies adjust to unpredictable trade conditions.
The Connection Between Tariffs and Currency Fluctuations
Tariffs don’t just affect the cost of goods, they also influence currency exchange rates, which in turn impacts the cost of your manufactured product. When a country imposes tariffs, it disrupts many things which alters the demand for different currencies and causes fluctuations in exchange rates. These shifts can make manufacturing either more expensive or more affordable, depending on how a country’s currency moves in response.
For example, when the U.S. imposed tariffs on Chinese imports in 2018, the Chinese yuan (RMB) weakened against the U.S. dollar. This depreciation partially offsets the impact of tariffs by making Chinese exports cheaper, helping Chinese manufacturers remain competitive despite the introduction of tariffs.
The relationship between tariffs and currency fluctuations can create unintended consequences for manufacturers. As discussed in Understanding the Impact of Tariffs on Exchange Rates and Production Costs, a weaker local currency can reduce production costs for exporters but increase costs for manufacturers that rely on imported materials priced in stronger foreign currencies. For example, a U.S. manufacturer sourcing components from Taiwan would see costs rise if the U.S. dollar weakens against the Taiwanese Dollar.
These currency fluctuations make it a bit more difficult when you are trying to price out your product. A company might adjust its pricing to account for tariffs, only to see those cost structures shift due to fluctuations in the exchange rate. As a result, businesses with a global supply chain must carefully monitor both tariffs and currency trends to anticipate cost changes and make informed sourcing decisions.
Relationship Between Pricing and Currency Fluctuations
For manufacturers with a global supply chain, pricing and currency fluctuations directly impact production costs, profit margins, and overall competitiveness. When exchange rates shift, the cost of raw materials, labor, and transportation can fluctuate unexpectedly, forcing manufacturers to continuously update their pricing.
Manufacturers sourcing components from overseas are particularly vulnerable to currency fluctuations. If a U.S. company imports parts from Europe and the euro strengthens against the dollar, those parts become more expensive, even if material costs remain unchanged. Similarly, when tariffs are introduced, currency values can adjust in response, adding another layer of unpredictability. As discussed in How Currency Fluctuations Affect Production Costs for Overseas Suppliers, even small shifts in exchange rates can lead to significant cost increases over time, impacting everything from supplier negotiations to retail pricing.
To mitigate these risks, manufacturers often diversify their supply chains or renegotiate their contracts to include pricing adjustments based on exchange rate movements. When you are using global suppliers, you need to understand the relationship between tariffs, pricing, and currency is essential for manufacturers looking to maintain cost stability and remain competitive in shifting market conditions.
Conclusion - How Tariffs Affect Manufacturing Costs
Tariffs, pricing, and currency fluctuations are deeply interconnected, shaping the costs that manufacturers face in a globalized economy. While tariffs directly increase the price of imported goods, their impact goes beyond taxes. They disrupt supply chains, influence sourcing decisions, and contribute to currency fluctuations that can either offset or amplify changes brought on originally by tariffs. As seen in past trade disputes, tariffs often trigger adjustments in exchange rates, affecting the cost of raw materials and production in ways that businesses must carefully navigate.
For manufacturers, these complexities highlight the importance of strategic planning. Monitoring currency movements, diversifying supply chains, and negotiating flexible pricing agreements can help mitigate the risks associated with tariffs and exchange rate fluctuations. While there is no one-size-fits-all solution, businesses that understand these dynamics will be better equipped to manage costs and maintain competitiveness in an ever-evolving trade landscape.
By staying informed and adaptable, manufacturers can turn these challenges into opportunities, leveraging currency trends to their advantage, optimizing sourcing strategies, and making data-driven decisions that ensure long-term stability.
Comments