Going from EVT to DVT to PVT: The Milestones You Need to Complete
- Jared Haw
- Mar 1
- 6 min read

The journey from product development to mass production is not as simple as finalizing a design and placing an order. A product must go through multiple validation processes to ensure it functions as intended, meets quality standards, and can be manufactured reliably at scale. This process is divided into three key phases: EVT (Engineering Validation Test), DVT (Design Validation Test), and PVT (Production Validation Test).
Each phase serves a specific purpose, from testing core functionality to making iterations during design for manufacturing. However, progressing from one stage to the next isn’t automatic; certain milestones must be met before moving forward. Skipping these milestones can lead to costly redesigns, production delays, or quality failures.
In this blog, we’ll briefly explain each phase but focus on the key milestones required to transition from EVT to DVT and from DVT to PVT. Understanding these checkpoints will help ensure a smoother path from development to mass production.
EVT: Engineering Validation Test
The Engineering Validation Test (EVT) is the first major milestone in transitioning a product from development to production. At this stage, the goal is to validate that the fundamental design works as intended and meets the necessary performance requirements. Prototypes built during EVT are typically made using rapid prototyping methods or early-stage manufacturing processes rather than final production tooling.
At this stage, you will not be opening up mass production tools but will 3D print prototypes instead.
Key Milestones in EVT
To move from EVT to DVT, the following milestones must be completed:
Core Functionality Validation
The prototype must demonstrate that all major features work as designed.
Electrical, mechanical, and firmware components should function together without critical issues.
If any major failures occur, the design must be revised and retested.
Electrical and Mechanical Testing
PCB validation ensures that the circuit board meets performance specifications.
Mechanical fit and structural integrity are assessed, verifying that components fit together correctly.
Thermal and stress testing may be performed to identify design weaknesses.
Firmware and Software Integration
Basic software functionality is tested with hardware to confirm compatibility.
Debugging begins, but full feature optimization is not yet expected.
Prototype Iterations and Design Refinements
Multiple prototype builds may be necessary to resolve initial issues.
Engineers make necessary design changes before locking in specifications for the next phase.
Passing Criteria to Move to DVT
A product can move from EVT to DVT only when it accomplishes the following:
✔ The core functionality is validated, and major design issues have been resolved.
✔ No significant electrical or mechanical changes are expected in future builds.
✔ The design is stable enough to begin testing for manufacturability.
Once these conditions are met, the product is ready for Design Validation Testing (DVT), where manufacturability, regulatory compliance, and reliability are put to the test.
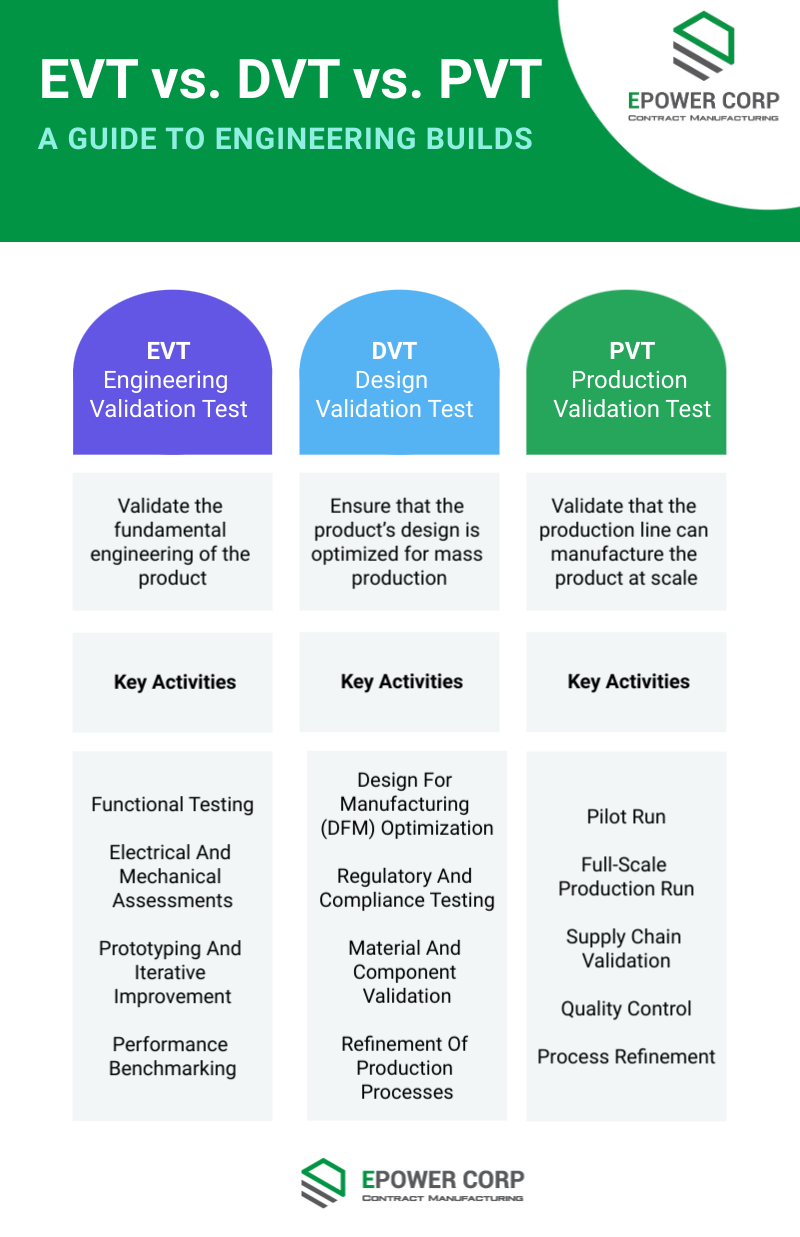
DVT: Design Validation Test
The Design Validation Test (DVT) phase ensures that the product is not only functional but also manufacturable at scale and compliant with all necessary standards. Unlike EVT, where design changes are still expected, DVT focuses on refining production methods and validating that the product meets aesthetic, regulatory, and durability requirements. At this stage, prototypes are built using production-intent materials, and early manufacturing processes are tested.
Key Milestones in DVT
To move from DVT to PVT, the following milestones must be completed:
Final Design Freeze
The product’s design must be locked, meaning no further mechanical, electrical, or firmware changes are expected.
Any last modifications to improve manufacturability must be completed at this stage.
Reliability and Compliance Testing
The product undergoes environmental, stress, and lifecycle testing to ensure it meets durability requirements.
Regulatory compliance testing (such as EMI/EMC, FCC, CE, or UL certification) is conducted to confirm the product meets industry standards.
Manufacturing Process Validation
Prototype units are built using production-intent tooling, materials, and manufacturing methods.
Assembly processes are tested to identify inefficiencies, quality risks, or yield issues.
Suppliers and contract manufacturers must demonstrate their ability to produce consistent, high-quality units.
Cosmetic and Material Approval
The product’s surface finishes, colors, and branding elements are reviewed to ensure they meet specifications.
Variability in appearance between units is assessed and controlled.
Packaging and Shipping Validation
Packaging is tested to confirm it protects the product during shipping and storage.
Drop tests and vibration tests may be performed to simulate real-world handling.
Passing Criteria to Move to PVT
A product is ready to move from DVT to PVT only when it accomplishes the following:
✔ The design is fully frozen, with no further changes required.
✔ The product has passed all required compliance and durability tests.
✔ Manufacturing processes are stable, and production yields are within acceptable limits.
✔ The final appearance and branding elements meet quality standards.
Once these criteria are met, the product advances to Production Validation Testing (PVT), where full-scale production readiness is assessed.
PVT: Production Validation Test
The Production Validation Test (PVT) is the final step before a product moves into full-scale mass production. At this stage, the goal is to ensure that the manufacturing process is capable of producing the product at scale, consistently, and with high quality. PVT focuses on validating the entire production line, identifying any inefficiencies or defects, and confirming that the product can be produced in large quantities without compromising quality.
Key Milestones in PVT
To transition from PVT to full-scale production, the following milestones must be achieved:
First Full Production Run
The first batch of units is produced on the full production line.
Testing begins to ensure that the product meets all quality specifications, such as mechanical tolerances, electrical functionality, and overall performance.
Any issues with the production process, such as bottlenecks, defects, or inefficiencies, are identified and addressed.
Quality Control and Inspection
Each unit undergoes rigorous inspection to verify that it meets all design specifications.
Detailed checks are performed for aesthetics, functionality, and any customer-specific requirements.
Statistical Process Control (SPC) techniques may be used to monitor the production line for consistency and quality.
Production Line Optimization
Any issues identified during the first production runs are addressed, such as tooling adjustments, assembly improvements, or material changes.
The production line is refined for efficiency and higher yield rates, ensuring the process can sustain high-quality output at scale.
Worker training is conducted to optimize assembly speeds, quality assurance processes, and production consistency.
Final Packaging and Logistics Validation
Packaging is tested for its ability to protect the product during shipping, handling, and storage.
Logistics testing may also be conducted to confirm that products can be delivered to customers efficiently and without damage.
Production Readiness Assessment
A full assessment is made to ensure that the product can be manufactured at scale without significant issues.
Final checks are made to verify that all supply chain components—materials, tooling, and labor—are in place and functioning as required.
Passing Criteria to Move to Mass Production
A product is deemed ready for mass production only when it accomplishes the following:
✔ The production process has been validated with minimal defects and inefficiencies.
✔ Quality control processes are robust, ensuring consistent product quality.
✔ Packaging and logistics processes are proven to protect the product and ensure timely delivery.
✔ Production lines are optimized for cost-effective, high-volume manufacturing.
Once these milestones are met, the product is fully validated for mass production, and it can now be released to the market with confidence in its performance, reliability, and manufacturability.
Conclusion: Going from EVT to DVT to PVT
Going from EVT to DVT to PVT is a crucial process in ensuring that a product is ready for the demands of full-scale production. Each phase, Engineering Validation, Design Validation, and Production Validation, plays a specific role in validating the product’s design, functionality, manufacturability, and quality. By meeting the key milestones at each stage, teams can confidently move from one phase to the next, minimizing the risk of costly delays, quality issues, or production failures down the line.
Skipping or rushing through any of these stages can lead to serious setbacks, so it’s essential to invest time and resources to thoroughly validate each phase. A well-executed EVT, DVT, and PVT process ensures that when your product finally hits the production line, it is ready for market success.
Understanding the importance of these milestones and carefully tracking progress at each stage is essential for bringing products to market efficiently, on time, and with the quality your customers expect.
Comments